Nur der Vollständigkeit halber ...die neuen Endkappen mit gekerbter Schnuraufnahme. Da scheuert nichts mehr.
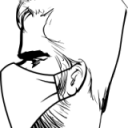
3D-Druck im Drachenbau
-
-
Wenn Du genau hinschaust, hat dein Bauteil einen Hohlraum in dem T-Abschluss. Mein Bauteil hat das nicht. Ob das jetzt besser oder schlechter ist, spielt hier jetzt keine Rolle. Es geht mir...
Hi dragidus,
auf dem Foto ist ein normaler PVC Gewebeschlauch zu sehen. Es ist kein gedrucktes Teil. Die Grundidee stammt aus Zeiten, wo an 3D Druck im privaten Bereich noch nicht zu denken war.
Grüße, Stefan
-
Hi dragidus,
auf dem Foto ist ein normaler PVC Gewebeschlauch zu sehen. Es ist kein gedrucktes Teil. Die Grundidee stammt aus Zeiten, wo an 3D Druck im privaten Bereich noch nicht zu denken war.Grüße, Stefan
Habe ich auch nicht behauptet, dass es sich bei dem Bauteil auf deinem Foto um einen 3D-Druck handelt. Spielt ja auch keine Rolle.
Zu meinem speziellen Fall gibt es hier schon die Auflösung des Rätsels:
Der erste Mirage-Fetisch Stammtisch
Das die Idee solcher Verbinder schon alt ist, spielt eben so wenig eine Rolle. Nur weil Dinge aus dem 3D Drucker stammen, muss das Bauteil nicht unbedingt innovativ sein.
Dieses Teil habe ich nur aus der Not heraus geboren, weil ich keine Lust habe, mehr Porto zu zahlen als das Bauteil selbst wert ist. Da es bei uns in Düsseldorf keinen gescheiten Drachenladen mit einer guten Grundausstattung an Ersatzteilen mehr gibt, musste der 3D Drucker herhalten. Da lohnt auch eine Fahrt nach Wuppertal nicht, weil die Spritkosten auch höher als die Bauteilkosten wären
Meine Idee war das Angenehme mit dem Nützlichen zu verbinden und das Bauteil exemplarisch für einen Materialtest hier aufzulisten.
Aber wenn man einen kleinen Stein ins Wasser wirft, können die Wellen erstaunlich hoch schwappen... und das alles nur wegen des hässlichen Textilbandes. -
Naja, das Textilband war halt in deiner Präsentation enthalten, mir hat das auch nicht besonders gefallen und ich denke, wenn man schon ein Teil am Rechner konstruiert und es leicht optimiert, dann sollte man sich halt Gedanken machen, wie es sauber gelöst wird. Ich hätte beispielsweise lieber am T-Ausleger wie du es nennst links und rechts je ein Loch eingebaut und dort die Schnur auf einer Seite durchgeführt, um den Ausleger gewickelt, durch das zweite Loch durchgeführt. So würde das Klettband die Schnur sichern. Es geht sicherlich auch deutlich besser, aber so wäre kein Textilband nötig, die Schnur würde die Endkappe sichern und das Klett die Schnur.
Ich persönlich fände es auch interessanter, wenn die Konstruktionen hier etwas innovativer wären und sich weniger am Vorhandenen orientieren würden, allerdings verstehe ich vollkommen, dass die 3D-Drucker-Besitzer sich vielleicht lieber auch über das verfügbare Material austauschen. Davon abgesehen werde ich mich hüten, Innovation zu "fordern", wenn ich mich nicht einbringen kann.
-
3D-Drucker-Bauer bin ich ( und daher besitze ich auch einen)
Aber das ist kein Grund, mit seiner Idee hinter dem Berg zu halten.
Vorschläge finde ich von allen Seiten willkommen. Wenn jemand Bauteile verbessern kann, dann die, die das Material später fliegen.Die erfahrenen Flieger wissen meist, wo Fehler liegen. Man muss das Rad nicht ständig neu erfinden. Aber neue Wege gehen ist mit 3D-Drucktechnik sehr verlockend.
Deine Idee ist super. Der einzige Nachteil ist der, dass die Schnur so wenig wie möglich der Reibung des Klettbandes ausgesetzt sein soll. Daher habe ich die Schnur im Rohr gesichert.
Das macht die Konstruktion stabil und verschleisfrei. Ich finde es nicht schlimm über solche Details zu reden, aber in diesem Thread geht es vorrangig um 3D-Druck im Allgemeinen.Zukünftig sollten in solchen Fällen einfach neue Threads zu diesen speziellen Fällen aufgemacht werden, um hier den Rahmen des Themas nicht zu sprengen.
-
Ich hatte ja selbst mal eine Mirage XL und XXL, ich fand die Elliot-Abspannung immer... nicht so toll. Original ist es ja so, dass man die Schnur um das Klett wickelt und dann durch Schließen des Klett sichert. So ziemlich alles ist besser als das, ich denke, es kommt auch etwas darauf an, wie oft man das Klett aufmachen möchte.
Ich spiele aber vor allem auch auf Spreizverbinder an beispielsweise. Bisher wurden vorhandene Verbinder skaliert und nachgedruckt, aber mit 3D-Druck gäbe es ja beispielsweise auch die Möglichkeit, dass man für jeden Drachen den Winkel der Spreizverbinder individuell druckt. Ebenso können die Verbinder mMn ruhig härter sein als z.B. APAs, wenn man entsprechend den richtigen Winkel wählt und die Spreizen beim Abbau herausnimmt. Beim Trickflug lassen wir die Spreizen aus Bequemlichkeit meist im APA, diese müssen durch ihre kurze Bauform entsprechend fest sitzen. Würde man die Spreizaufnahme länger machen und evtl. konifizieren, so könnte man die Spreizen auch leichter rausnehmen, ohne dass man Gefahr läuft, dass die Spreizen im Flug rausfallen.
Die Vorhandenen Teile sind ja alle schön und gut, aber viele Formen sind sicherlich auch dem Umstand geschuldet, dass die Teile eben per Spritzguss oder in der Drehbank hergestellt werden mussten. Nach dem was ich gehört habe, wie teuer die Formen für die Spritzgussmaschine sind, verstehe ich vollkommen, dass man dann einfach mal 10 oder 20 Jahre dieselben Verbinder produziert, anstatt Verbesserungen einfließen zu lassen. Es funktioniert ja auch alles, aber beim 3D-Druck hat man diese Grenzen eben nicht.
-
Stimmt prinzipiell. Aber 3D-Drucker sind ursprünglich nur für reines Prototyping gebaut worden. Die Robustheit von Kunststoffteilen aus dem Spritzgussverfahren wird man im 3D-Druck nicht erreichen ( zumindest nicht bei FDM 3D-Druckern für den Heimanwender).
Ganz abgesehen davon, das ein 3D-Drucker für eine industrielle Nutzung in der Massenproduktion wenig bis gar keinen Sinn macht.
Wenn man wie in meinem Fall ein Provisorium druckt und ganz nebenbei kleine Änderungen im Design ausprobiert, kann das aber eventuell für die Industrie mal interessant werden, wenn sich das neue Produkt als haltbarer erweist als die bisher verwendete Technik. Trotzdem ist es immer gut, wenn von der "Basis", also den aktiven Drachenfliegern, neue Ideen kommen, die dann schnell umgesetzt werden können. Für das Design der Verbinder muss man nicht so viel Zeit investieren wie bei komplexen Maschinen wie etwa 3D Drucker
Das mit den individuell angepassten Winkeln der Spreizverbinder ist z. B. eine sinnvolle Idee, die Länge zu ändern eher nicht. Bei diesen Teilen muss man immer auch das Gewicht im Auge behalten, um einen möglichst großen Windbereich abdecken zu können.
Es macht keinen Sinn, teure Tücher, die ultra leicht sind, zu verwenden, um dann schwergewichtige Verbinder einzubauen. Wenn es gelingt, das Gewicht durch geeigneten Infill zu reduzieren bei Verlängerung der Verbinderrohre, wäre das natürlich wieder anders.
Um die dauerhafte Stabilität solcher neuen Designs aber sicher auszutesten, müsste man möglichst viele Drachenflieger finden, die sich als Betatester zur Verfügung stellen. So einfach ist es also leider nicht. -
Ich spreche ja nicht von Massenfertigung von Drachenbauteilen per 3D-Druck, ich meine eher, dass man die Vorlagen teilt, anpasst und dann selbst druckt oder drucken lässt. Du hast deine Verbinder wegen Porto-Ersparnis gedruckt, aber es gibt auch ganz andere handfeste Gründe, z.B., dass bestimmte Verbinder einfach gar nicht verfügbar sind, aus welchem Grund auch immer.
Ich habe vorhin von einem Projekt gelesen (Werbung von Solidworks), bei dem Muffen für einen Fahrradrahmen aus Metall gedruckt wurden und damit dann Carbonrohre zu einem Rahmen verbunden wurden. Im Artikel stand, dass die Rahmengeometrie über die Parameter in einer Excel-Tabelle angepasst werden kann, welche dann vom Programm ausgelesen wird. Dadurch kann man dann über die Maße in der Exceltabelle im Endeffekt verschiedene Rahmentypen (Mountainbike, Cityrad, Rennrad...) und -größen herstellen, ohne komplett neu zu konstruieren. So in etwa wäre es ja für jedem mit vertretbarem Aufwand möglich, seine Verbinder an den Drachen anzupassen, ohne jedesmal neu zu kontruieren. Natürlich braucht man die passende Software, ich weiß auch nicht, inwiefern das praktikabel ist für Endanwender, die kleinteile für ein paar Euro drucken wollen, aber das klang sehr interessant.Beim Windbereich spielen noch ganz andere Dinge als 3g Gewicht pro uQS-Verbinder rein, aber gut, die Diskussion gehört hier nicht hin.
-
Was du meinst ist parametrisches Design. Das kann man bei Winkelverbindern relativ einfach erreichen. Die Verbinder sind dann skalierbar in Länge, Durchmesser, Wandstärke, Winkel, Anzahl der Verbindungsrohre etc.
Die Software dafür gibt es bereits und ist in viele CAD-Programme integriert. Persönlich nutze ich OpenScad. Das ist ein ideales Werkzeug zum Erstellen parametrischer Designs. Weiterer Vorteil: Es ist quelloffen, d.h. jeder kann es kostenlos herunterladen, nutzen und verbessern.
Es ist allerdings ein sehr spezielles CAD-Programm, das ein gewisses Mass an Programmierkenntnissen voraussetzt, also nichts für reine Mausbenutzer. Für Endanwender macht das aus meiner Sicht keinen Sinn, solange es keine einfach und intuitiv zu benutzende Oberfläche oder etwas wie von dir Beschriebenes dafür gibt. Der Aufwand steht m.E. in keinem Verhältnis zum Nutzen.Abgesehen davon würde das den wenigen noch existierenden Drachenläden noch mehr das Wasser abgraben, weswegen ich so etwas nie aktiv entwickeln würde (obwohl ich es könnte).
Es gibt im Netz bereits verschiedene Ansätze für so konstruierte Verbinder, ist also schon Ansatzweise brauchbar.
Sinnvoll für stabile Verbinder ist auch die Verwendung von mehreren unterschiedlichen Filamenten. Da wäre es auch mal interessant, eine Datenbank mit Infos und Bildern aufzubauen, in der zerstörte Verbinder gezeigt werden mit drr Beschreibung, wie es zu dieser Zerstörung kam. Dann könnte man an den potentiellen Bruchstellen ein steiferes Filsment verwenden als an denen, die elastisch genug sein müssen, um die Stäbe problemlos einschieben und wider herausziehen zu können. Das lässt sich mit einem Werkzeugwechsler oder einer speziellen Druckdüse für mehrere Filamente heutzutage schon relativ einfach realisieren.
-
Um die dauerhafte Stabilität solcher neuen Designs aber sicher auszutesten, müsste man möglichst viele Drachenflieger finden, die sich als Betatester zur Verfügung stellen. So einfach ist es also leider nicht.
Ich plane gerade einen 2-Leiner bei dem die käuflichen Winkelverbinder wahrscheinlich nicht passen werden. Außerdem schwebt mir eine Verbindungsvariante zwischen Leitkante und Segellatte vor bei der ich flache, breite Verbinder aus weichem, elastischen Material brauche.
Als Betatester für Filamentmaterial wäre das sozusagen eine Win-Win Situation. Ich bekäme die passenden Verbinder und du den MaterialtestGruß Carsten
-
-
Der Carsten hat wohl doch kein Interesse gehabt.
Heute habe ich endlich mal Zeit gehabt, um das Ninjatek TPU anzutesten. Als Testobjekt habe ich mir in OpenScad eine Halterung für einen Spülschwamm gebaut, der mit Hilfre eines Saugnapfes an den Kacheln festgemacht werden kann.
Nach ein paar Schichten habe ich den Druck abgebrochen, um die Eigenschaften des Materials zu testen. Das Material ist extrem gut verdruckbar und hat wirklich sehr gute Eigenschaften in Bezug auf Flexibilität und Druckfestigkeit.Externer Inhalt youtu.beInhalte von externen Seiten werden ohne Ihre Zustimmung nicht automatisch geladen und angezeigt.Durch die Aktivierung der externen Inhalte erklären Sie sich damit einverstanden, dass personenbezogene Daten an Drittplattformen übermittelt werden. Mehr Informationen dazu haben wir in unserer Datenschutzerklärung zur Verfügung gestellt. -
Doch Doch!
bin nur noch nicht dazu gekommen ich melde mich bei dir.
Gruß carsten -
-
Habe gerade eine interessante Info gefunden. Ein italienischer Softwarearchitekt aus dem Bereich Flugzeugbau von der Uni Padua hat einen Online customizer für OpenScad entwickelt, mit dem man innerhalb einer Stunde ein funktionstüchtiges Gerüst für einen Minigleiter ausdrucken kann. Dieses Gerüst kann per customizer namens SOL75 online bearbeitet und nach eigenen Wünschen angepasst werden. Man kann sich das 3D Modell anschliessend herunterladen und ausdrucken.
Das soll in Zukunft mit einer Fülle von Anwendungsbereichen und Objekten funktionieren.Die Besonderheit dabei ist, dass nicht nur parametrisierte Objekte zum Einsatz kommen, sondern auch Materialbeanspruchung und Normwerte etc. in die Kalkulation des Modells einfliessen.
Die Projektseite Sol75 und der SOL75Gleiter -
Hallo zusammen,
ich werde auch bald einen 3D-Drucker haben, den ich vorwiegend für den Modellbau nützen werde. Da ich aber auch Drachen baue, hatte ich überlegt, ob man damit nicht auch die Verbinder für einen Hargrave-Drachen oder einen Bell-Tetraeder drucken könnte? Ich hatte mir vor 15(?) Jahren mal Hargrave-Verbinder von Lutz Treczoks aus Alu gekauft. Tolle Qualität, aber jetzt natürlich nicht mehr lieferbar. Und das wäre doch ein "Klacks" mit einem 3D-Drucker, oder? Das wäre dann eine Einmalgelegenheit, und genau dafür sind 3D-Drucker doch hervorragend geeignet.
Auf Thingiverse habe ich aber noch nichts gefunden; auf der anderen Seite sind das ja im Prinzip einfache Sachen; man müsste noch ein paar Stege gegen die Biegekräfte vorsehen, aber dann sollte das doch machbar sein. Und für 85€, was die Aluverbinder damals gekostet haben, kann man eine Menge Filament verdrucken.Bernhard
-
Konstruiere die halt mal und Berichte wie das Gewichtsverhältnis zu den Aluverbindern aussieht, also ob dieses vernachlässigbar ist.
-
-
-